Customer health and safety
Quality Basic Policy |
Basic Philosophy The Bando Group shall establish its product policy on the basis of social needs. In all facets of business activities, products, and services centering rubber / plastic products and system products including rubber / plastic products, everyone's originality, ingenuity, and ability to act are assembled to implement continual improvement in order to satisfy customer needs and expectations. Action Guidelines (1)Promote design, manufacturing, and sales activities that are committed to providing clients with quality that is "useful," "trustworthy," and "satisfying." (2)Establish zero-defects processes. Continuously improve the effectiveness of the quality management system to accomplish (1) and (2). |
---|
Material issue Customer health and safety
-
Targets/Vision
- ● To comply with regulations and voluntary codes on safety and health of products and services
- ● To completely understand components contained in raw materials purchased
Management and Promotion Method of Customer health and safety
[Responsible Departments]
- Quality Control Department of Manufacturing Planning Center
- Business divisions
[Policy/Point of view]
Recognizing safety of products and services as a top priority quality issue, the Group clearly states it in the “Group Code of Conduct” and also established the “Quality Policy,” based on which the “Quality assurance system” systematically defines what needs to be done in each stage, from understanding customer needs to sale, and the “Quality management system” governs the quality management after the start of mass production. Any failure is handled as a matter of the highest priority according to a rule whereby the person in charge is required to promptly reports it to the management, officer in charge of quality and other relevant parties, followed by an effort to prevent recurrence.
[Targets/Vision]
Comply with regulations and voluntary codes on health and safety of products and services
[Measures]
- Provide quality education
- (1) Hold workshops for QCC basic education, etc. organized by Quality Control Department
- (2) Ensure that all employees understand quality assurance
Provide new recruit education, engineer education, and Manufacturing School as well as level-based education
[Responsible Departments]
- Procurement Department of Manufacturing Planning Center
- Research Laboratories for Core Technologies of Manufacturing Planning Center
- Engineering divisions
Coordinating office: Safety and Environmental Promotion Department of Manufacturing Planning Center
[Policy/Point of view]
The Group stipulates the preservation of the global environment in the “Group Code of Conduct” and the pollution prevention in the “Environmental Basic Policy.” Chemical substances in raw materials are managed based on the “Standard for Preparation of rules and manuals: Raw material standard.” For regulated chemical substances, the Constituent Material Subcommittee of the Technical Committee identifies, determines how to handle and promotes replacement.
[Targets/Vision]
Identify 100% of the components contained in raw materials
purchased
Not to use internally prohibited substances
Manage chemical substances designated by laws and regulations, etc. in manufacturing
process as well as products and services
Manage chemical substances contained in products
[Measures]
- Conduct an inspection when business divisions procure materials
- Establish a system to manage contained chemical substances
- Promote replacement of substances subject to management/systematic reduction
Reduction of chemicals that may adversely affect the environment and human health
Our products use many chemical substances as raw materials and secondary materials. As some of them are feared to have adverse impact on the environment and human health, we are systematically reducing their use. In fiscal 2023, we continued to work to gradually replace certain phthalate esters (DOP, DBP) subject to RoHS Directive*¹ with alternatives to reduce chemical substances that are feared to have adverse impact on the environment and human health. As for the replacement of MOCA*² which is on the authorization list of REACH*³, the basic design for the alternative formulation has been completed, and we are now preparing for the replacement. We worked to eliminate lead from metallic materials before the end of the transitional period in July 2024 stated in the regulation under the RoHS Directive that restricts the use of lead in metallic materials.
*1RoHS Directive: European Union’s Directive on the restriction of the use of certain hazardous substances in electrical and electronic equipment *2REACH: Regulations by the European Parliament and the Council on Registration, Evaluation, Authorization and Restriction of Chemicals *3MOCA: Abbreviation of 3, 3’-Dichloro-4,4’-diaminodiphenylmethane. Used as hardener, etc. for polyurethane resin |
![]() |
---|
Compliance with regulations/voluntary codes on safety and health of products and services
The Bando Group systematically performs self-audit of in-house
operations and audit of suppliers and business partners to identify and address issues
as preventive measures. In order to comply with recent regulations on environmental load
substances, we conduct inspection of contained chemical substances not only for main raw materials but also for secondary
materials such as production tools and packing materials and are establishing necessary
systems.
Our efforts to promote safe and appropriate use of automotive power
transmission belts include sharing examples of various incidents attributable to belts,
explaining the inspection procedures and the correct installation method and
distributing an abrasion gauge to check the necessity of replacement at the exhibitions
for auto technicians sponsored by car parts dealers. In addition, videos explaining when
the belt should be replaced are available in eight languages on the official YouTube
channel for Bando in an effort to disseminate the knowledge.
In fiscal 2023, there
has been no violation of regulations on safety and health of products and services that
results in serious penalty or sanction.
Quality control management
In order to satisfy our customers, our group is striving to provide
products and services that meet the needs of customers "safety, environment, quality,
delivery time, and cost" requirement. The Company has received certification audit for the quality management system (ISO9001, IATF16949, and ISO13485) for our quality control system from design/development to mass production/sales. Certain subsidiaries made self-declarations of compliance with ISO9001 while receiving audit of Bando’s Quality Control Department, making efforts for continued improvement.
Also, to facilitate and ensure product development, we implemented an electronic document circulation system for application, review and approval mainly in Japan at first and then expanded it to five overseas affiliates after fiscal 2022. We will expand and roll out the system to other group companies while monitoring the effects.
The Group's basic idea is “voluntary inspection,” requiring the person (or department) who brought up to quality to check the results themselves. Through this self-inspection, we confirm the results of our work instantaneously on our own and minimize problems by expediting the necessary processing quickly. In other words, we conduct inspections with inspection items, standards and methods that are clearly determined for each manufacturing process, and not only troubles of our own process but also the defects of products flowing from the previous process are found and fed back.
●Acquisition of quality management system certification in Japan
Division | Item | Certification number |
---|---|---|
Industrial Products Business | Power transmission belts, power transmission systems, rubber conveyor belts, light-duty resin conveyor belts and its conveyor units, construction materials, rubber floor material for railroad car | ISO9001 |
Automotive Parts Business | Automotive Raw Edge V-Belts, V-ribbed belts, Automatic Tensioners, toothed belts | IATF16949 |
Advanced Elastomer Products Business |
OCA for automotive display | IATF16949 |
OA equipment parts, optoelectronics products, power transmission belts, high-performance coating films, plastic films/sheets and their complex | ISO9001 | |
New Businesses Promotion Center | High thermal conductive sheets, die-attach pastes, conductive inks, elastic strain sensors | ISO9001 |
Medical Device Business Promotion Department, New Businesses Promotion Center | Manufacturing of medical measuring device | ISO13485 |
●Acquisition of quality management system certification by domestic affiliates
Company name | Item | Certification number |
---|---|---|
Bando Industrial Components & Services, Ltd. | Hiroshima Sales Group, Chu-Shikoku Branch (sale of rubber and resin industrial products), North Kanto Sunline Processing Cente r and Samukawa Processing Center (manufacturing and manufacturing control of light-duty conveyor resin belts) | ISO9001 |
BL Autotec, Ltd. | Design, manufacturing, and sale of machinery, equipment, and parts of industrial automated products and robot-related products | ISO9001 |
Fukui Belt Industries, Ltd. | Manufacturing of industrial flat belts | * |
Aimedic MMT Co., Ltd. | Design, development, manufacturing, and sale of implants and instruments for orthopaedic surgery, motor function testing instruments and biosignal measuring devices Manufacturing and sale of thermal bone disinfection apparatus, fixation device, and pneumatic massaging tools Repair of instruments for orthopaedic surgery, thermal bone disinfection apparatus and fixation device Distribution of implants for dentistry |
ISO13485 |
* Fukui Belt Industries, Ltd. has not obtained certification by a certification body but made a self-declaration of compliance with ISO9001.
●Acquisition of quality management system certification in overseas
Company name | ISO9001 | IATF16949 |
---|---|---|
Bando USA, Inc. | ○ | - |
Bando Korea Co., Ltd. | - | ○ |
Bando Jungkong Ltd. | ○ | - |
Bando Belt (Tianjin) Co., Ltd. | ○ | ○ |
Bando Manufacturing (Dongguan) Co., Ltd. | ○ | - |
Bando Manufacturing (Vietnam) Co., Ltd. | ○ | - |
Bando Manufacturing (Thailand) Ltd. | ○ | ○ |
Bando (India) Pvt. Ltd. (Bengaluru) | - | ○ |
Bando (India) Pvt. Ltd. (Delhi) | - | ○ |
Bando Belt Manufacturing(Turkey), Inc. | ○ | ○ |
Bando Europe GmbH | ○ | - |
Bando Iberica, S.A. | ○ | - |
Sanwu Bando Inc. | ○ | - |
Kee Fatt Industries, Sdn. Bhd. | ○ | - |
PT. Bando Indonesia | ○ | ○ |
Philippine Belt Manufacturing Corp. | ○ | - |
Early response to defects in the market
The Bando Group deals with all customer complaints with complete sincerity regardless of whether the Group is responsible for them. To ensure quick response to customer complaint, we have established a rule whereby any customer complaints must be promptly reported to top management, quality assurance executive, and other relevant personnel and deal with them as a matter of top priority. To eradicate customer complaints, we are working on preventive and recurrence preventive measures, such as self-audit activities, and ensure to follow basic principles under the established rules. | ![]() |
---|
QC (Quality Control) Circles
Bando started QC activities more than 50 years ago, and each site now has an administrative committee focused on continuing voluntary improvement activities, particularly in manufacturing. QC Circle activities originate with and are implemented by circle members to increase awareness and capabilities, and to educate future leaders. The goal is to increase customer satisfaction and make a social contribution through a bright, vibrant and meaningful workplace.
Additionally, each year we hold QC Circle Presentations at our sites in ASEAN on a rotating basis, with one circle from Bando also making a presentation. These presentations are also a good opportunity for plant tours and information exchange.
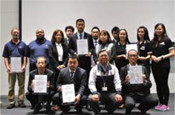
Presentations at Bando
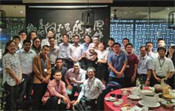
ASEAN QC Circle
Presentations
(Taiwan is pictured)