Product Quality Control
Quality Policy
Basic Philosophy
The Bando Group will establish a product policy based on the needs of society. The Bando Group will conduct business activities centered on rubber and plastic products, and system products including those products, and all facets of supplying products and services, and will concentrate the originality, ingenuity, and ability to take action of all employees and, by implementing continuous improvement, satisfy customer needs and expectations.
Action Principles
- 1. Promote design, manufacturing, and sales activities devoted to the supply of ‘helpful’, ‘trusted’, ‘happiness inducing’ quality to clients.
- 2. Establish zero-defect processes.
Quality control management
In order to satisfy our customers, our group is striving to provide products and services that meet the needs of customers "safety, environment, quality, delivery time, and cost" requirement. The process from grasping customer's needs to selling is classified into 5 steps "market research and planning, product design, production / sales design, mass production / sales preparation, mass production / sales". The roles of each division and collaboration among divisions are systematically compiled as a quality assurance system, and after mass production, quality assurance activities that conform to the quality management system will enable you to supply good products to customers.
The Group's basic idea is "voluntary inspection"by the person (or department) who incorporated the quality checks. Through this self-inspection, we confirm the results of our work instantaneously on our own and minimize problems by expediting the necessary processing quickly. In other words, we conduct inspections with inspection items, standards and methods that are clearly determined for each manufacturing process, and not only troubles of our own process but also the defects of products flowing from the previous process are found and fed back.
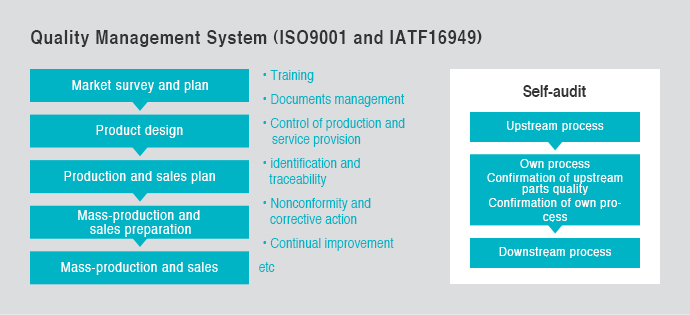
Quality Management System (ISO9001 and IATF16949)
QC (Quality Control) Circles
Bando started QC activities more than 50 years ago, and each site now has an administrative committee focused on continuing voluntary improvement activities, particularly in manufacturing. QC Circle activities originate with and are implemented by circle members to increase awareness and capabilities, and to educate future leaders. The goal is to increase customer satisfaction and make a social contribution through a bright, vibrant and meaningful workplace. Additionally, each year we hold QC Circle Presentations at our sites in ASEAN on a rotating basis, with one circle from Bando also making a presentation. These presentations are also a good opportunity for plant tours and information exchange.
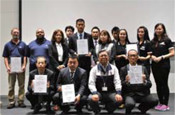
Presentations at Bando
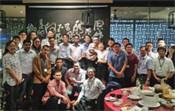
ASEAN QC Circle Presentations (Taiwan is pictured)
Early response to defects in the market
The Bando Group treats all customer complaints with complete sincerity, even if the attribution for the complaint is still unclear. We have established rules, applicable from management through those responsible for and associated with the quality particular products, and top priority is given to a quick and reliable response to customer complaints.
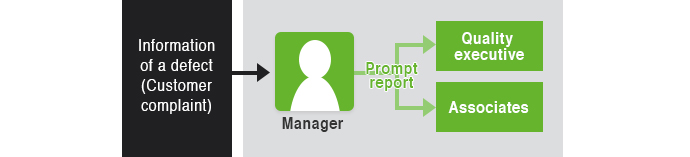
Top priority
Quality Management System
Sixteen of our domestic divisions and overseas business locations have received ISO9001 certification, while 10 of our domestic and overseas business locations have obtained IATF 16949 certification.