Product/process innovations
Material issue Product/process innovations
- Targets/Vision
- ●The ratio of Environmentally-Friendly Products and Products with Fewer Hazardous Substances among the total newly marketed products: 50% or more (fiscal 2026)
- ●Labor productivity: Double Loss: 50% Capital productivity: Double
Management and Promotion Method of Product/process innovations
[Responsible Departments](Product)
- Engineering divisions
- Engineering Department of New Businesses Promotion Center
- Research laboratories
Coordinating office: Technical Committee (Secretariat: Technology Planning Group of Research Laboratories for Core Technologies)
[Policy/Point of view]
The “Group Code of Conduct” stipulates the preservation of the global environment, and the “Environmental Basic Policy” aims at saving resources and energy and reducing wastes and hazardous substances in each of the stages of technology development, design, procurement, production, sale, and use of products and services. In addition, we are working to develop high-functional, energy-saving, and low-environmental impact products meeting market needs.
[Targets/Vision]
Ratio of environmentally-friendly products among the total newly marketed products: 50% or more (fiscal 2026)
[Measures]
Products to be developed are checked against the “Environmental Instruction and Design Standards” at the time of proposal, registered as environmentally-friendly products for a development theme by the Technical Committee and monitored for its progress. When the development is completed, the products are reviewed by the Eco-moving Subcommittee of the Technical Committee and registered as environmentally-friendly products to appeal to customers and society.
[Responsible Departments] (Process)
- Manufacturing Technology Development of Manufacturing Planning Center
- Manufacturing technology divisions of business divisions
[Policy/Point of view]
The Group develops the manufacturing methods that care for the global environment and people in the mid-term management plan CV-1 as the innovation of manufacturing is essential to grow our core businesses globally and improve profitability.
Guideline 2: Creation of smart manufacturing, Development of smart manufacturing methods
[Targets/Vision]
Labor productivity: Double
Energy productivity: Double
Environmental impact productivity: Double
[Measures]
- Prepare for the Bando Dream Factory through the mid-term management plan CV-1
Manufacturing Technologies Development Department, Manufacturing Planning Center: Develop elemental technologies and manufacturing methods to improve labor and energy productivity
Manufacturing technology department of business divisions: Develop smart manufacturing methods for specific products
Product Innovation: Expand “Environmentally-Friendly Products”
We have focused on developing belt products for automotive and other industries for years and refined our energy-saving related technologies by sincerely addressing needs of customers and society. Currently, our private brand of environmentally-friendly products “eco moving” and products that satisfy at least 50% of the baseline values for key Environmental Claims that define this brand, and Products with Fewer Hazardous Substances are grouped into the “Environmentally-Friendly Products” category, and we are working to expand it. By fiscal 2022, the final year of BF-2, we aim to increase the ratio of “Environmentally-Friendly Products” to 50% or more of newly marketed products.
In fiscal 2021, we launched 47 new “Environmentally-Friendly Products” including “BANDO GLANMESSE™ Chromatic Laminate Films (Gloss Finish),” laminate films for signboards and signage materials, which reduced CO2 emissions by approximately 21% compared to the existing products by reducing weight through thin film manufacturing technologies, achieving approximately 65% in the ratio of “Environmentally-Friendly Products” among the total newly marketed products.
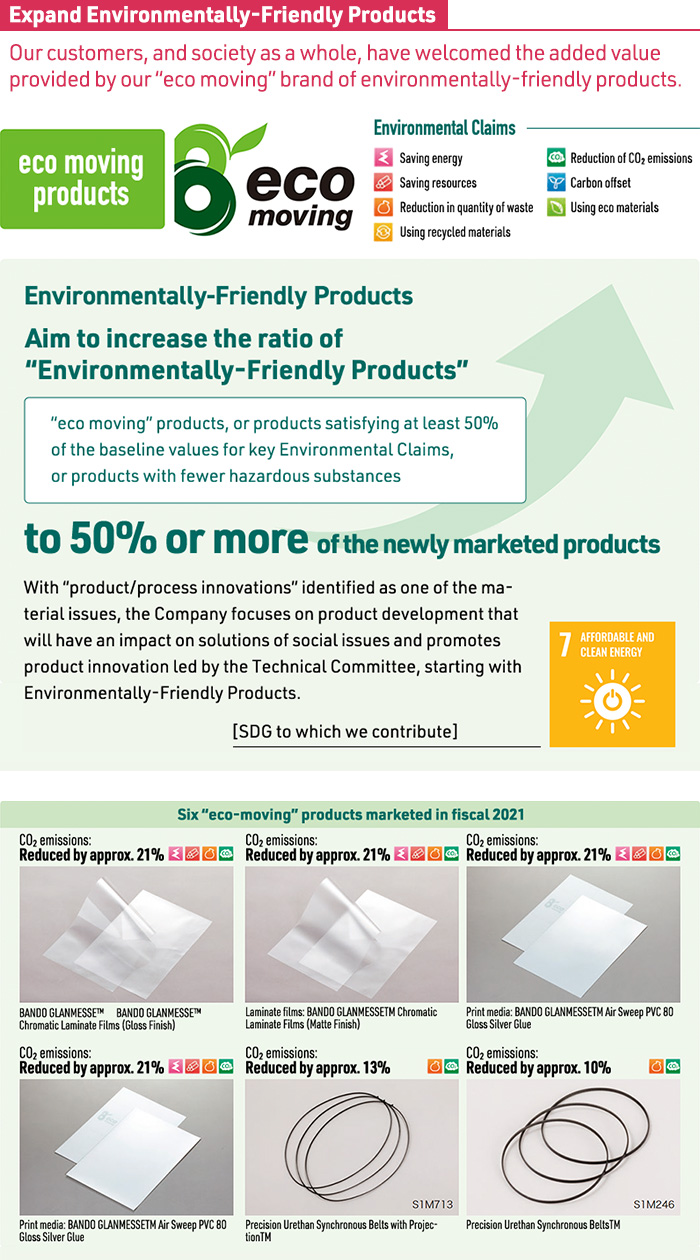
[Other Environmentally-Friendly Products]
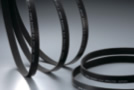
Environmental consideration at the time of disposal Transmission belts using non-chlorinated synthetic rubber.
1.Saving energy

The product’s energy loss during use is cut by 15% or more, in comparison with the corresponding reference product.
2.Saving resources

The raw materials used for the product are reduced by 10% or more by mass, in comparison with the corresponding reference product.
3. Reduction in quantity of waste

Product-related waste during use is reduced by 10% or more by mass, in comparison with the corresponding reference product.
4. Using recycled materials

The product uses 20% or more recycled materials by weight.
5. Using eco materials

The product uses 80% or more eco materials by weight (recycled materials as well as non-petrochemical natural resources and materials).
6. Reduction of CO2 emissions

The product reduces CO2 emissions by 10% or more during its lifecycle, in comparison with the corresponding reference product. Or, the product reduces CO2 emissions by 15% or more during any stage of its lifecycle (material procurement, production, transportation, use, disposal).
7. Carbon offset

The product is certified by the carbon offset certification system (third party institution), and the appropriate carbon offset activities have been implemented.
Contributing to downsizing/high efficiency/ high performance of electronic devices
“Thermal Management” products that apply core technologies
In recent years, demand for "downsizing,” “high efficiency,” and “high performance” of electronic devices has been increasing at an accelerated pace in various fields due to the full-scale application of IoT and edge computing to the telecommunications industry in addition to the spread of the next-generation semiconductors in power devices used in automobiles, railways, and new energies, etc. To meet these demands, efficient “thermal management” that actively “controls heat” is indispensable, and it also requires an elaborate thermal design as well as high-performance electronic materials to realize it.
The Company has applied our core technologies, including the rubber and elastomer processing technologies developed from “dispersion technology,” to develop products that suppress heat generation by enhancing heat dissipation effects with a combination of orientation technology and nanoparticle generation technology and has produced optimal electronic materials for thermal management. We have developed and manufactured “distinctive products” that can solve customers’ issues in manufacturing electronic devices, including “HEATEX™,” a high thermal conductive sheet that has achieved ultra-high thermal conductivity using boron nitride as thermally conductive filler, and "FlowMetal™,” a silver nanoparticle bonding material paste which can be bonded at low temperatures and without pressurization.
CASEInquiries for HFD system™ increased as products contributing to carbon neutrality
Its high energy-saving performance (reduction of power consumption by an average of 7%) that maximizes the transmission efficiency of flat belts was valued, and in fiscal 2021 the number of inquiries increased by approximately 150% year-on-year mainly for the use in blowers and air conditioners.
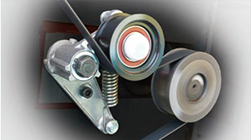
HFD System™
Process Innovation: Improve labor productivity and reduce material loss and energy consumption through development of new production method
Under the guideline of “Enhancement and Evolution in Manufacturing” set in the mid-to-long term business plan BF-2, we promote the development of innovative production methods of main products. We are working on significant reduction of wastes and energy consumption through the development of new production methods. Please see here for details.
* The Company defines innovative production methods as production methods that achieve any of the followings: double labor productivity, halve loss, or double capital productivity compared with the conventional methods.
Improve precision and efficiency of the compounding design using material design simulation by quantum chemical calculations
We use the quantum chemical calculations to model material structures on the molecular level and clarify how physical properties appear through simulations.
Compared to the conventional methods that evaluate physical properties by test productions or experiments based on past knowledge and experiences, this new material design method can not only increase development speed but also further improve performance through a theoretical approach such as comparing and verifying simulation and experiment results.
* We use a supercomputer of Foundation for Computational Science (“FOCUS”) for the quantum chemical calculations.
Optimized structure
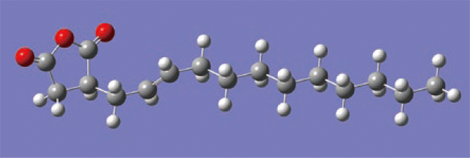
Comparison of IR spectrum
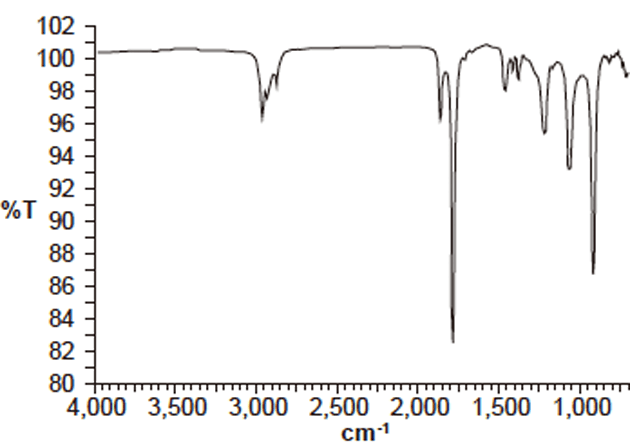
Experiment results
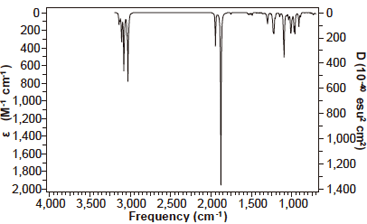
Simulation results
Development of visual inspection device using AI
The Bando Group has been promoting the application of AI to manufacturing sites to raise the level of SEQDC (Safety/Environment/Quality/Delivery/Cost) of our products. In fiscal 2019, we started the application of AI to part of the visual inspection. We will continue the development to overcome issues in the visual inspection including “it takes time to foster inspection workers,” “inspection results varies depending on inspection workers,” and “inspection takes manhours” while aiming at flexible response to changes in production volume. We will also broaden the scope of AI application to various manufacturing sites in addition to the visual inspection device.
TOPICSChallenge to new production method of accessory drive power
transmission belts for automobiles
Under the new production method, characteristics of materials have a greater impact on product features (results) than the conventional method. Although we had difficulty setting conditions for stable processing, young development team members combined their expertise and repeated tests, achieving the reduction of material loss by more than 60% and the improvement of resource productivity. The newly developed and introduced heating method, for which we obtained a process patent, can reduce energy consumption by more than 50% compared to the conventional method and also contributes to the improvement of working environment. We were able to shorten the processing time by dividing processes in the line with the new production method and improve labor and capital productivity by introducing robots for transferring, attaching and detaching molds.
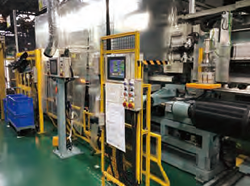
TOPICSDevelopment of transparent PVC films used to
prevent droplet infection
The starting point of the development of transparent PVC films used to prevent droplet infection is that our sales division was quick to learn about the shortage of transparent films for partition in the market as they were used as preventive measures against COVID-19. Although the Company had not manufactured soft PVC films to be used for partition before then, we used our existing technologies (analysis, compounding design, architectural design, and manufacturing) and facilities and developed transparent PVC films used to prevent droplet infection in a short term. The products require high visibility (transparency) and “flexible” workability. High transparency requires mirror surface design, but the existing design and production methods made films sticky. This issue was quickly solved as relevant departments put their heads together to improve from the aspects of compounding design, architectural design and manufacturing technology. We sold these developed films through leading home improvement store chains and also donated to communities where our offices are located. We also use them in our offices.
To supply needed products as soon as possible, all departments from manufacturing to sales worked together and contributed to easing the product shortage in the market.

PVC films installed in the office to prevent droplet infection
Contributing to reduction of industrial waste and energy consumption
The establishment of a new production method for urethane belts also enables to reduce industrial waste through reduction of urethane material loss and also reduce energy consumption resulting from shortened crosslinking time and a change of the heating method.
TOPICSPursue further potential of urethane
materials through
a new production method
In order to establish a new production method, we utilized urethane material
technology, one of our core technologies, and designed unique compounding of
urethane materials which will be the base. As the handling of the urethane materials
with new compounding was difficult, we fundamentally reviewed the manufacturing and
design conditions of the belt itself. After a number of trial and error, we finally
established manufacturing conditions and solved various technical issues, and
consequently, we successfully developed a production method enabling to improve
labor and capital productivity and reduce material loss.
The belts made of urethane materials with new compounding exhibit the durability
three times higher than that of conventional products and are also more
cost-efficient as they require a fewer number of molds to manufacture. We will
continue to work on “Enhancement and Evolution in Manufacturing” mainly with our
main power transmission belt products and pursue further potential.
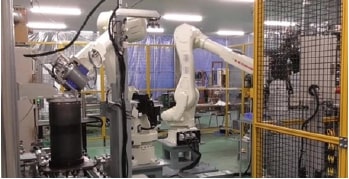