Water and effluents / Emission /
Waste
Safety and disaster readiness
Material Issue Water and effluents
- Targets/Vision
- ● Management of total water withdrawal per water source by actual value
- ● Maintain the quality of water discharge below the standards set by local governments
Management and Promotion Method of Water and effluents
[Responsible Departments]
- Manufacturing Planning Center
- Business divisions
Coordinating office: Environment Committee (Secretariat: Safety and Environmental Promotion Department of Manufacturing Planning Center)
[Policy/Point of view]
The Group sets forth the preservation of the global environment in the “Group Code of Conduct” and the
“Environmental Basic Policy” and strives to save resources and energy and reduce wastes and hazardous
substances in each stage of technology development, design, procurement, production, sale, and use of
products and services. We recognize the importance of water resource that is essential for our
production activities and launched initiatives to confirm and reduce water risk.
As for the volume of water consumption, each business manages the total water withdrawal by source.
As for effluents, each business facility checks the volume and quality of water discharge to comply with the standards set by relevant local governments.
[Targets/Vision]
- Manage the total water withdrawal per water source by actual value
- Maintain the quality of water discharge below the standards set by local governments
[Measures]
- Manage the total water withdrawal per water source at each business facility
- Check the volume and quality of water discharge at each business facility
Launched an initiative to understand and reduce water risk
Although none of the Group’s production bases is currently located in areas with water restriction, we recognize the importance of water resource that is essential for our production activities and launched an initiative to understand and reduce water risk in fiscal 2018. Based on the research of total water withdrawal per water source for our domestic and overseas production bases, the total water withdrawal in fiscal 2020 was 1,174,176m³.
Going forward, we will identify water discharge channels in domestic and overseas offices having production divisions to further reduce water risk and conserve water resources.
●Total water withdrawal (Fiscal 2018 to 2020)
Total/Water source(m3/year) | Total /Discharge(m3/year) | |||||
---|---|---|---|---|---|---|
Fiscal 2018 | Fiscal 2019 | Fiscal 2020 | Fiscal 2018 | Fiscal 2019 | Fiscal 2020 | |
Bando Chemical Industries | 927,756 | 873,749 | 788,816 | 268,831 | 264,750 | 199,412 |
Domestic affiliates | 4,422 | 3,748 | 6,396 | 1,436 | 1,239 | 1,279* |
Overseas affiliates | 315,712 | 384,961 | 378,964 | 173,425 | 211,366 | 83,169* |
The entire Group | 1,247,890 | 1,262,458 | 1,174,176 | 443,692 | 477,355 | 283,861 |
* The calculation method of water discharge was changed in fiscal 2020.
Compliance with our voluntary standard for quality of discharged water
The quality of water discharge of production base is managed using the voluntary standard set stricter than those set by relevant local governments.
The Group’s production bases have in place a system to stop discharging water and collect it when abnormality is found in water quality in daily operations, but recently, heavy rains that cause massive damages are becoming more frequent, raising the risk of leakage or effluence of contaminants, wastes, and liquid raw materials. Nankai Plant installed oil film detectors in drainage and cooling water tank as a measure to early prevent effluence of contaminated water and prevent damage in the environment and community surrounding the Plant. Ashikaga Plant has installed water quality monitoring equipment to early detect and respond to abnormalities as it discharges water used in its production process and cafeteria, etc. to river via a purifying chamber. Kakogawa Plant raised oil weir of oil-water separation paths, and Wakayama Plant implemented measures to prevent rainwater ingress into and waste oil leaks at the industrial waste storage.
Material Issue Emission
- Targets/Vision
- ● Reduce CO2 emission intensity by 20% from the fiscal 1990 level by 2020
Management and Promotion Method of Emission
[Responsible Departments]
- Manufacturing Planning Center
- Business divisions
Coordinating office: Environment Committee (Secretariat: Safety and Environmental Promotion Department of Manufacturing Planning Center)
[Policy/Point of view]
The Group sets forth the preservation of the global environment in the “Group Code of Conduct” and the
“Environmental Basic Policy” and strives to save resources and energy and reduce wastes and hazardous
substances in each stage of technology development, design, procurement, production, sale, and use of
products and services.
Recognizing the seriousness of the escalation of climate change issues, the Company aims at reducing
CO2 emissions which is one of the aggravating factors for climate change risks, and has implemented
various initiatives such as shifting to different fuels, switching to high-efficiency equipment and
LED lighting, and installing high-efficiency boilers at business facilities, in addition to
aggressively adopting modal shifts, joint deliveries, and milk run logistics. We are also proactively
adopting new methods such as ESCO service and Joint Crediting Mechanism.
The Company has set a long-term target for the reduction of CO2 emissions, with the actual results
managed by each business facility.
[Target]
Bando Chemical Industries’ target for fiscal 2030: 33,915t-CO2t (reduction by 38% from the fiscal 2013 level) | |
Bando Group target for fiscal 2050: | Carbon Neutrality |
[Measures]
- 1. Enhance energy management technology through trainings for energy management engineers
- 2. Use external energy-saving diagnosis and energy-saving patrol to check the effects and consider improvements
- 3. Improve energy efficiency of facilities by fully considering energy-saving at the time of new installation or renewal
Initiatives for CO2 emission reduction
In fiscal 2020, we reduced CO2 emissions by 30% compared to the fiscal 1990 level, achieving the fiscal 2020 target.
We are aiming to reduce CO₂ emissions from our business activities by 18% compared to the fiscal 2013 level by fiscal 2030.
Although CO2 emissions in fiscal 2020 decreased 34% from the fiscal 2013 level, the significant decrease is temporary and CO2 emissions will increase as production volume recovers. So, we recognize that we need to further promote energy saving of equipment and buildings to achieve the fiscal 2030 target.
※Fiscal 2030 Target
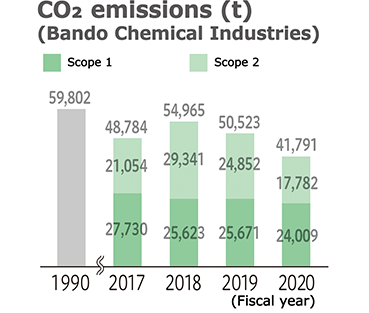
*Based on the 2005 emission factors of the electric power supplier, published by the Ministry of the Environment
Scope 1: Direct emissions by the Company from use of fuel, etc.
Scope 2:Indirect emissions from power stations, etc. associated with the consumption of electricity purchased by the Company
Reduction of VOC emissions
Volatile organic compounds (VOC) are considered as major causal substances of photochemical oxidants and are subject to the voluntary reduction effort under the Clean Air Act.
We work to reduce VOC with enhancements to the processing equipment, and proper handling and storage of the compounds. We set our voluntary reduction targets at 55% reduction from the fiscal 2000 level, which was higher than the industry target of 50%, and achieved it in fiscal 2012. Since then, we have been reducing emissions at levels exceeding this target. In fiscal 2020, we achieved a 76% reduction compared with the fiscal 2000 level.
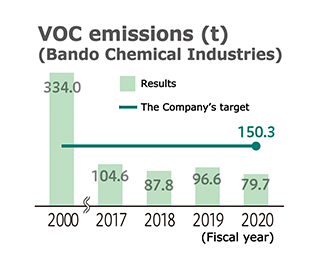
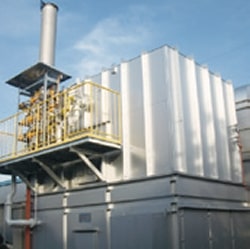
VOC processing equipment
Initiatives to reduce environmental impact in logistics
We are working on improving transport efficiency and lightening packing in order to reduce environmental impact arising from material procurement and product shipment as well as transportation of intermediate products between production bases. We are also promoting such initiatives as joint deliveries, milk run logistics, and modal shifts with an aim to reduce CO2 and NOx emissions generated by freight transport.
Material Issue Waste
- Targets/Vision
- ● Achieve reduction target of waste generation
Management and Promotion Method of Waste
[Responsible Departments]
- Manufacturing Planning Center
- Business divisions
Coordinating office: Environment Committee (Secretariat: Safety and Environmental Promotion Department of Manufacturing Planning Center)
[Policy/Point of view]
The Group sets forth the preservation of the global environment in the “Group Code of Conduct” and the
“Environmental Basic Policy” and strives to save resources and energy and reduce wastes and hazardous
substances in each stage of technology development, design, procurement, production, sale, and use of
products and services.
For waste, each business facility checks the waste generation to comply with the standards set by relevant local governments.
[Visions]
- Reduction target of waste generation (annual)
[Measures]
- Check the waste generation at each business facility
Achieve zero emissions
We have already achieved zero emissions* through thorough waste separation. We will continue to work on reducing waste generation for the efficient use of resources.
*Definition of zero emissions: Final landfill disposal rate of less than 1% (final landfill disposal rate = final landfill disposal volume/volume of waste generation)
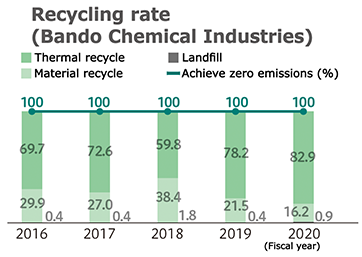
Emissions and transfer volumes of PRTR substances
We designated substances specified in the PRTR* (Pollutant Release and Transfer Register) as controlled substances and are striving to reduce their use by shifting to alternatives while maintaining proper management.
*Pollutant Release and Transfer Register (PRTR) system: A system whereby business operators are required to identify the amount of chemical substances potentially hazardous to human health and ecosystems emitted from the plants into the environment (air, water, and soil) and the amount transferred out of the plants as part of the wastes and report them to the government, which then aggregates and publishes the emitted/transferred amounts based on the submitted data and estimates.
The fiscal 2019 volumes in the chart below was retrospectively revised from the actual emitted/transferred volumes disclosed in CSR Report 2020 to those submitted to the government.
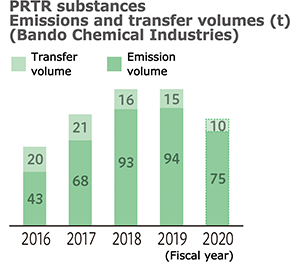
Material Issue Safety and disaster readiness
- Targets/Vision
- ● Claims, accidents or emergencies: None
Management and Promotion Method of Safety and disaster readiness
[Responsible Departments]
- Each business facility
Coordinating office: Company-Wide Health and Safety Committee (Secretariat: Safety and Environmental Promotion Department of Manufacturing Planning Center)
[Policy/Point of view]
As the Company is engaged in manufacturing while interacting with society and local communities, we established the “Group Code of Conduct” and the “Health and Safety Policy” to set forth the compliance with the environmental laws and regulations and agreements with the local governments and industries, and are striving to prevent pollution in society and local communities with the target of achieving “No claims, accidents or emergencies.”
[Targets/Vision]
Claims, accidents or emergencies: None
[Measures]
- Maintain the latest version of the environmental laws and regulations and agreements with local communities that are applicable to business facilities in accordance with the “Environmental Guidelines”
- Evaluate each business facility’s status of compliance with the applicable environmental laws and regulations, etc. in accordance with the compliance assessment of the “Environmental Manual”
- Provide education to employees using textbooks incorporating past incidents
- Participate in security and disaster readiness activities in local communities/Hold meetings for local residents near business facilities
To prevent claims, accidents or emergencies
The Group is engaged in manufacturing while interacting with society and community and aims at “No claims, accidents or emergencies” by enhancing initiatives to prevent them.
In fiscal 2020, there were one claim (PRTR error report at Kakogawa Plant) and three accidents (two small fires at Nankai Plant and one leakage of chemical substance at a domestic production base), and we pursued the cause, established measures and implemented them across the Group to prevent recurrence. In fiscal 2020, we refrained from holding briefing sessions and monitor meetings for local residents, which we hold annually, due to COVID-19. Instead, we conducted a telephone survey of local residents at Nankai Plant and conducted a survey and distributed environment monitoring documents that summarized measurement results, etc. of the environmental data at Kakogawa Plant.
In addition, we reflected the latest environmental laws and regulations as well as agreements with local communities in the “Environmental Guidelines” and “Environmental Manual” and also provided education using past incidents. We will continue to aim at “No claims, accidents or emergencies.”
Security and disaster readiness activities
We also focus on security and disaster readiness activities in preparation for emergencies to ensure business continuity and safe operation. Specifically, the Bando Group suffered massive damages to its Head Office and production bases from the Great Hanshin-Awaji Earthquake, and therefore we continue to work on creating disaster-resistant working places.
- Earthquake countermeasures and emergency drills, etc.
In addition to antiseismic reinforcement to the buildings at domestic offices, we introduced an emergency earthquake notification system in its Head Office and conduct drills to ensure employees can take initial responses in a very limited time before an earthquake occurs. Usually, group offices would conduct joint drills with local fire stations or brigades, and Nankai Plant would cooperate with emergency drills in which local residents participate every year. The Head Office would hold “Memorial walk for earthquake disaster” every year on the anniversary day of the Great Hanshin-Awaji Earthquake, with participants walking for about 50 minutes from the Head Office to Sannomiya to check the evacuation route at the time of disaster. In fiscal 2020, however, all of these events were cancelled due to COVID-19. - Memorial walk for earthquake disaster
The Company holds “Memorial walk for earthquake disaster” every year on the anniversary day of the Great Hanshin-Awaji Earthquake. Participants walk for about 50 minutes from the Head Office in Port Island to KOBE EAST PARK in Sannomiya and check the evacuation route at the time of disaster and a route from Port Island to Sannomiya.
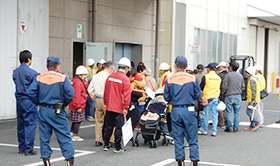