Customer health and safety
Quality Basic Policy |
Basic Philosophy The Bando Group shall establish its product policy on the basis of social needs. In all facets of business activities, products, and services centering rubber / plastic products and system products including rubber / plastic products, everyone's originality, ingenuity, and ability to act are assembled to implement continual improvement in order to satisfy customer needs and expectations. Action Guidelines (1)Promote design, manufacturing, and sales activities that are committed to providing clients with quality that is "useful," "trustworthy," and "satisfying." (2)Establish zero-defects processes. Continuously improve the effectiveness of the quality management system to accomplish (1) and (2). |
---|
Material issue Customer health and safety
-
Targets/Vision
- ● To comply with regulations and voluntary codes on safety and health of products and services
- ● To completely understand components contained in raw materials purchased
Management and Promotion Method of Customer health and safety
[Responsible Departments]
- Quality Control Department of Manufacturing Planning Center
- Business divisions
[Policy/Point of view]
Recognizing safety of products and services as a top priority quality issue, the Group clearly states it in the “Group Code of Conduct” and also established the “Quality Policy,” based on which the “Quality assurance system” systematically defines what needs to be done in each stage, from understanding customer needs to sale, and the “Quality management system” governs the quality management after the start of mass production. Any failure is handled as a matter of the highest priority according to a rule whereby the person in charge is required to promptly reports it to the management, officer in charge of quality and other relevant parties, followed by an effort to prevent recurrence.
[Targets/Vision]
Comply with regulations and voluntary codes on health and safety of products and services
[Measures]
- Provide quality education
- (1) Hold workshops for QCC basic education, etc. organized by Quality Control Department
- (2) Ensure that all employees understand quality assurance
Provide new recruit education, engineer education, and Manufacturing School as well as level-based education
[Responsible Departments]
- Procurement Department of Manufacturing Planning Center
- Research Laboratories for Core Technologies of Manufacturing Planning Center
- Engineering divisions
Coordinating office: Safety and Environmental Promotion Department of Manufacturing Planning Center
[Policy/Point of view]
The Group stipulates the preservation of the global environment in the “Group Code of Conduct” and the pollution prevention in the “Environmental Basic Policy.” Chemical substances in raw materials are managed based on the “Standard for Preparation of rules and manuals: Raw material standard.” For regulated chemical substances, the Constituent Material Subcommittee of the Technical Committee identifies, determines how to handle and promotes replacement.
[Targets/Vision]
Identify 100% of the components contained in raw materials
purchased
Not to use internally prohibited substances
Manage chemical substances designated by laws and regulations, etc. in manufacturing
process as well as products and services
Manage chemical substances contained in products
[Measures]
- Conduct an inspection when business divisions procure materials
- Establish a system to manage contained chemical substances
- Promote replacement of substances subject to management/systematic reduction
Reduction of highly toxic chemicals
Our products use many chemical substances as raw materials and secondary materials. As some of them are feared to be toxic to environment and human health, we are systematically reducing the use of them. In fiscal 2021, we continued to work to replace certain phthalate esters (DOP, DBP) subject to RoHS Directive*¹ and MOCA*² which is on the authorization list of REACH*³. For phthalate esters, we conducted a comprehensive review, including the content in the raw materials as well as contamination during the manufacturing process, in consideration of their migration characteristics. For MOCA, we selected and examined several alternatives based on the information collected form material manufacturers and the compounding study.
We worked to eliminate lead from metallic materials before the end of the transitional period in July 2024 stated in the regulation under the RoHS Directive that restricts the use of lead in metallic materials.
*1RoHS Directive: European Union’s Directive on the restriction of the use of certain hazardous substances in electrical and electronic equipment *2REACH: Regulations by the European Parliament and the Council on Registration, Evaluation, Authorization and Restriction of Chemicals *3MOCA: Abbreviation of 3, 3’-Dichloro-4,4’-diaminodiphenylmethane. Used as hardener, etc. for polyurethane resin *4Masterbatch: Antimony trioxide solidified using various resins |
![]() |
---|
Compliance with regulations/voluntary codes on safety and health of products and services
The Bando Group systematically performs self-audit of in-house
operations and audit of suppliers and business partners to identify and address issues
as preventive measures. In order to comply with recent regulations on environmental load
substances, we conduct inspection not only for main raw materials but also for secondary
materials such as production tools and packing materials and are establishing necessary
systems.
Our efforts to promote safe and appropriate use of automotive power
transmission belts include sharing examples of various incidents attributable to belts,
explaining the inspection procedures and the correct installation method and
distributing an abrasion gauge to check the necessity of replacement at the exhibitions
for auto technicians sponsored by car parts dealers. In addition, videos explaining when
the belt should be replaced are available in eight languages on the official YouTube
channel for Bando in an effort to disseminate the knowledge.
In fiscal 2021, there
has been no violation of regulations on safety and health of products and services that
results in serious penalty or sanction.
Quality control management
In order to satisfy our customers, our group is striving to provide
products and services that meet the needs of customers "safety, environment, quality,
delivery time, and cost" requirement. The Company has received certification audit for the quality management system (ISO9001, IATF16949, and ISO13485) for our quality control system from design/development to mass production/sales. Certain subsidiaries made self-declarations of compliance with ISO9001 while receiving audit of Bando’s Quality Control Department, making efforts for continued improvement.
The Group's basic idea is "voluntary inspection" by the person (or department) who
incorporated the quality checks. Through this self-inspection, we confirm the results of
our work instantaneously on our own and minimize problems by expediting the necessary
processing quickly. In other words, we conduct inspections with inspection items,
standards and methods that are clearly determined for each manufacturing process, and
not only troubles of our own process but also the defects of products flowing from the
previous process are found and fed back.
●Acquisition of quality management system certification in Japan
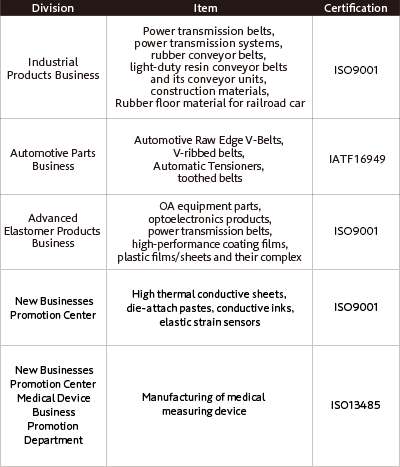
●Acquisition of quality management system certification by domestic affiliates
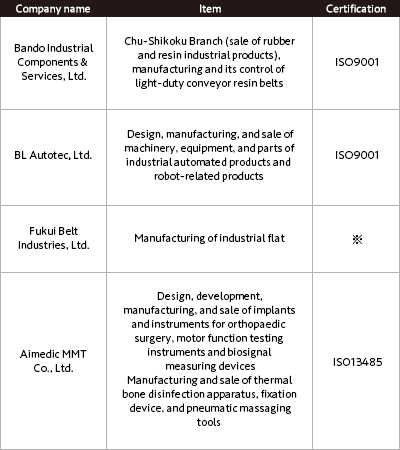
*Fukui Belt Industries, Ltd. has not obtained certification by a certification body but made a self-declaration of compliance with ISO9001.
●Acquisition of quality management system certification in overseas
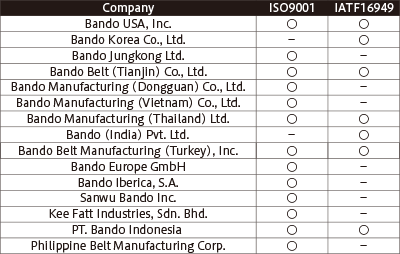
Early response to defects in the market
The Bando Group deals with all customer complaints with complete sincerity regardless of whether the Group is responsible for them. To ensure quick response to customer complaint, we have established a rule whereby any customer complaints must be promptly reported to top management, quality assurance executive, and other relevant personnel and deal with them as a matter of top priority. To eradicate customer complaints, we are working on preventive and recurrence prevention measures, such as self-audit activities, and ensure to follow basic principles under the established rules. | ![]() |
---|
Aimedic MMT Co., Ltd., our group company, conducted a voluntary product recall
Sterile packaging defects which might affect the sterility of the products were detected in some cables used to fix medical devices inside the body, and therefore Aimedic voluntarily recalled the products. No reports of health damage related to this event have been received.
QC (Quality Control) Circles
Bando started QC activities more than 50 years ago, and each site now has an administrative committee focused on continuing voluntary improvement activities, particularly in manufacturing. QC Circle activities originate with and are implemented by circle members to increase awareness and capabilities, and to educate future leaders. The goal is to increase customer satisfaction and make a social contribution through a bright, vibrant and meaningful workplace.
Additionally, each year we hold QC Circle Presentations at our sites in ASEAN on a rotating basis, with one circle from Bando also making a presentation. These presentations are also a good opportunity for plant tours and information exchange.
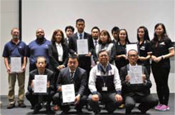
Presentations at Bando
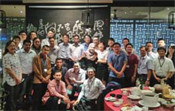
ASEAN QC Circle
Presentations
(Taiwan is pictured)