Materials/ Energy
Material Issue Materials
- Targets/Vision
- ● Reduce intensity of raw material input to below the best value in the past three years
* Excluding fiscal 2020 (as a decrease in production volume due to COVID-19 resulted in outliers)
Management and Promotion Method of Materials
[Responsible Departments]
- Business divisions
- Manufacturing Planning Center
Coordinating office: Planning Department of Manufacturing Planning Center
[Policy/Point of view]
The Group sets forth the preservation of the global environment in the “Group Code of Conduct” and the “Environmental Basic Policy” and strives to save resources and energy and reduce wastes and hazardous substances in each stage of technology development, design, procurement, production, sale, and use of products and services.
[Targets/Vision]
Intensity of raw material input: Below the best value in the past three years
[Measures]
- Use intensity (raw material-related wastes/raw material input) as a management indicator and set reduction target for intensity, with the monthly results of each business facility managed by the Company-Wide Environment Committee.
- Promotion method: Set a reduction target for failure and loss for each line, set an agenda for reduction and promote improvement.
Use of raw materials without waste
The Company’s industrial waste largely consists of rubber and plastics. As rubber is difficult to reuse, the Company strives to reduce waste primarily by curbing waste generation at manufacturing sites. As initiatives to reduce wastes related to existing products, we promote manufacturing that does not reduce efficiency even in small batch customization through production planning and process improvement, in addition to reducing loss and defective products through day-to-day improvement activities.
In fiscal 2020, the total volume of raw material-related wastes decreased because of a decrease in production volume due to COVID-19, but raw material input intensity increased.
In fiscal 2021, in addition to the activities continuing from fiscal 2020, we will further promote the product development and new production methods considering the waste reduction from the designing stage.
*Definition of zero emissions: Final landfill disposal rate of less than 1% (final landfill disposal rate = final landfill disposal volume/volume of waste generation)
Raw material-related wastes, intensity of raw material input (Bando Chemical Industries)
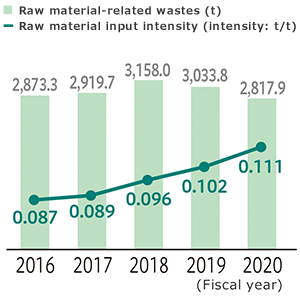
Material Issue Energy
- Targets/Vision
- ● Reduce five-year average of raw material input intensity by 1% or more every year
Management and Promotion Method of Energy
[Responsible Departments]
- Manufacturing Planning Center
- Business divisions
Coordinating office: Company-Wide Environment Committee (Secretariat: Safety and Environmental Promotion Department of Manufacturing Planning Center)
[Policy/Point of view]
The Group sets forth the preservation of the global environment in the “Group Code
of Conduct” and the “Environmental Basic Policy” and strives to save resources and
energy and reduce wastes and hazardous substances in each stage of technology
development, design, procurement, production, sale, and use of products and
services.
For energy, each business facility manages energy consumption based on an annual
reduction target.
[Targets/Vision]
Reduce energy consumption (KL)/Raw material input (t) from the previous year’s level, and decrease the 5-year average reduction rate by 1% or more (consistent with the target of the Energy Conservation Act)
[Measures]
- 1. Enhance energy management technology through trainings for energy management engineers
- 2. Use external energy-saving analysis and energy-saving patrol to check the effects and consider improvements
- 3. Improve energy efficiency of facilities by fully considering energy-saving at the time of new installation or renewal
Reduce energy consumption
Our initiatives to reduce energy consumption include conducting energy saving patrols whereby we check the improvement activities and energy usage in the production processes and give guidance to cut energy waste and engaging external energy management experts to get an energy saving diagnosis, based on which we implement systematic measures. In fiscal 2020, we focused especially on energy saving with equipment and buildings, and therefore upgraded substation transformers to high efficiency ones at Nankai Plant, Kakogawa Plant, and Ashikaga Plant and reinforced heat insulation of steam pipes at Nankai Plant. At Ashikaga Plant, we renewed the purifying chamber with the subsidies granted by the Ministry of the Environment, and it was determined that Nankai Plant will receive subsidies to promote energy-saving investment. In addition, all business locations are switching to LED lighting systematically.
In fiscal 2020, however, because of the spread of COVID-19, we had to suspend part of the production and energy use efficiency decreased significantly, and therefore we were not able to achieve the target for energy consumption intensity.
Energy consumption per volume of raw material input (Bando Chemical Industries)
Introducing renewable energy
The Company actively uses renewable energy. We started introducing solar power generation systems gradually in our domestic plants since fiscal 2010. Ashikaga Plant sells electricity that it generates to the Tokyo Electric Power Company Group and others using Japan’s feed-in tariff (“FIT”) scheme for renewable energy.
● Energy production in 2019
Business facilities introduced solar power generation systems | Wakayama Plant | Kakogawa Plant | Nankai Plant | Ashikaga Plant |
---|---|---|---|---|
Solar cell capacity (kW) | 150 | 160 | 200 | 1,750 |
Annual energy production (thousand kWh) | 145 | 171 | 263 | 2,527 |
*Electricity generated at Ashikaga Plant (BANDO eco moving Ashikaga solar power facility) is sold to the Tokyo Electric Power Company Group through our group company and others using the FIT system for renewable energy.
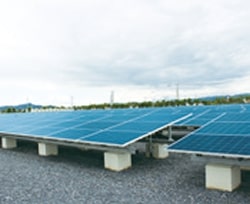
Solar panels at the BANDO eco moving solar power facility
TOPICSApproach to environmentally-friendly office
As part of our group-wide initiative to switch to LED lighting, in fiscal 2020, we switched the lighting of the office building at Head Office to LED lighting, reducing annual power consumption by 91,110kWh. Since fiscal 2019, the Head Office has participated in “Kansai Eco Office,” an activity organized by Union of Kansai Governments which registers offices engaging in environmental activities such as energy saving as “environmentally-friendly offices.” Our efforts include using recycled water for toilet, dissolving paper waste such as unnecessary documents (recycled as toilet paper) and collecting/recycling cardboard boxes and used paper. In addition, all employees made a united effort to promote eco-office initiatives including the “Cool/Warm Biz campaigns” which maintain the room temperature at 28℃ in summer and 19℃ in winter with employees working in comfortable clothes throughout the year and the movements to automatically turn off the light and let in external light from windows during lunch break and to use stairs instead of elevators. In local community, we participated in a “Social experimentation of common boarding pass,” which encourages to use bus instead of Port Liner to mitigate congestion of Port Liner, by Kobe City in order to avoid the three C’s (closed spaces, crowded places, and close-contact settings) amid the COVID-19 pandemic. | ![]() LED lightening of the office building at Head Office |
---|
TOPICSTOPICS: Head Office declared as Kansai Eco Office
The Company declared its further engagement in environmental activities as
an “environmentally-friendly office” in April 2019. “Kansai Eco Office” is
an activity undertaken by Union of Kansai Governments, which registers
offices engaging in environmental activities such as energy saving as an
“environmentally-friendly office.” Our efforts in fiscal 2019 included appropriate temperature setting of air conditioners, promotion of summer/winter eco-friendly fashion and electricity saving, switching to LED lighting, introduction of energy-saving/new energy equipment, promotion of green purchasing, waste recycling, and enlightenment activities for employees. By switching mercury light at workplace of the laboratory building to LED lighting, we were able to reduce power consumption by approximately 62%. Also, LED lighting is well-received by employees as it takes a shorter time to light up than mercury light. We will continue to promote energy saving and also work to realize pleasant working environment. |
![]() LED lighting of the laboratory building at Head Office |
---|
TOPICSSwitch to high-efficiency equipment and LED lighting system
At Ashikaga Plant, we employed the Ministry of the Environment’s
ASSET* to switch to a power generator that uses city gas instead of heavy oil and
air conditioning equipment that uses waste hot water from the generator, and also
introduced LED lighting. The subsidy is granted for CO2 emission control measures
subject to the introduction of certified products using leading and low-carbon
technology. We started to work on the concept in 2015 and it took us three years to
evaluate profitability and finalize the plan to apply for the subsidy and finally
complete the plan.
The new power generator provides most of the electricity used by the plant (half in
the summer and two-thirds in the spring, fall and winter). In fiscal 2018, such
equipment replacements and shift to LED lighting reduced CO2 emissions by
1,606.9t-CO2, or over 19.5% of the annual CO2 emissions at Ashikaga Plant.
* ASSET: Advanced technologies promotion Subsidy Scheme with Emission reduction Targets
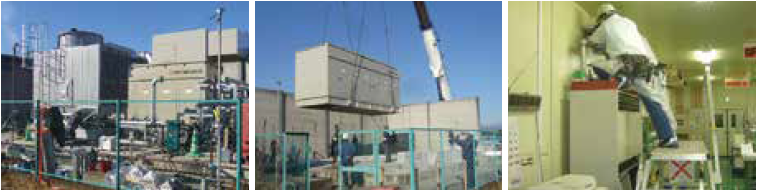
Improvement of Energy management technology
We have energy management training for energy managers to learn about equipment and design energy saving equipment for manufacturing.
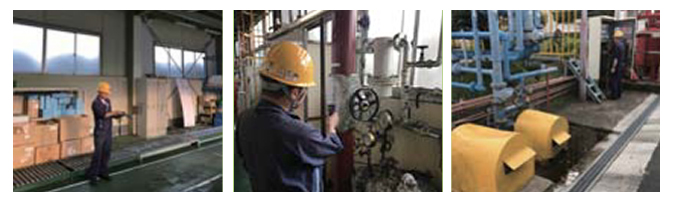