Occupational safety
Safety and Health Basic Policy
Basic Philosophy
The Bando Group shall conduct its business based on respect for human dignity and promotes continuous improvement in safety and health management activities, by mobilizing the originality, ingenuity and energy of all employees, to ensure our own safety and health.
Action Principles
- 1. Bando and its employees shall comply with all applicable laws and regulations relating to occupational safety and health, as well as any rules in place at particular places of business and shall strive to prevent work-related injuries and diseases and contribute to the maintenance and improvement of health.
- 2. Bando shall recognize that it is directly responsible for preventing work-related injuries and diseases and establish an occupational safety and health management system. Under the proper implementation and operation of this system in conjunction with its employees, Bando shall create a safe, pleasant work environment.
- 3. Bando and its employees shall be actively and voluntarily involved in safety and health activities to protect our own safety and health by mobilizing the originality, ingenuity, and energy of all employees.
- 4. Bando shall inform all employees of the Safety and Health Basic Policy and drive its continuous improvement activities by annually reviewing and updating, as appropriate, the Safety and Health Policy, in response to changes or new conditions in safety and health activities or depending on the results of management system audits.
Material Issue Occupational safety
Targets/Vision
- ●Work-related injuries resulted in no lost time or more: None (Non-consolidated and domestic affiliates)
- ●Work-related injuries resulted in lost time: None (Global target)
Management and Promotion Method of Occupational safety
[Responsible Departments] Safety
- Manufacturing Planning Center
- Business facilities
Coordinating office: Company-Wide Health and Safety Committee (Secretariat: Safety and Environmental Promotion Department of Manufacturing Planning Center)
[Policy/Point of view]
Recognizing that it is our responsibility to create a safe and comfortable workplace, the Group established the “Group Code of Conduct” and “Health and Safety Policy” to set health and safety targets and is striving to create a safe and comfortable workplace with the cooperation of our employees.
[Targets/Vision]
- Work-related injuries resulted in no lost time or more: None (Non-consolidated and domestic affiliates)
- Work-related injuries resulted in lost time: None (Global target)
[Measures]
The Company-Wide Health and Safety Committee and each business facility discuss matters related to health and safety regularly based on the established safety targets.
- 1. Promote safety measures through risk assessment Japan and overseas: All new facilities are subject to risk assessment
- 2. Reduce human errors through health and safety education
- 3. Conduct health and safety patrols
Overseas: Conduct facility inspection based on the examples of health and safety measures and the facility safety standards - 4. Handle chemical substances appropriately and manage them according to the Environmental Guidelines
Health and Safety Trends
Since FY2005, we have received Occupational Health and Safety Management System (JISHA method OSHMS) certification at each of our domestic production bases. We have developed health and safety risk assessments, accident and near miss activities, and risk forecast activities.
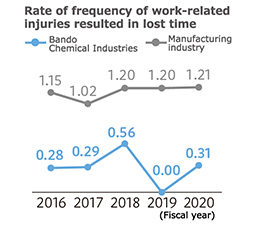
Major initiatives in fiscal 2020
❶Implementation of risk assessment and reduction of risks of level Ⅲ or higher
❷Re-establishment of operation manual
❸Improvement of safety sensitivity
❹Enhancement of health and safety patrols
❺Further vitalization of overseas affiliates’ activities
❻Improvement of road safety awareness
- OSHMS Certification
Ashikaga Plant, Wakayama Plant, Nankai Plant, Kakogawa Plant - ISO45001 Certification
Sanwu Bando Inc. P.T. Bando Indonesia
Bando Manufacturing (Thailand) Ltd. Bando Belt Manufacturing (Turkey), Inc.
Bando (India) Pvt. Ltd. Bando Korea Co., Ltd. Bando Belt (Tianjin) Co., Ltd.
Aiming at enhancing safety awareness and safety sensitivity
-
Promotion of risk assessment
We have completed risk assessment for a cumulative total of approximately 7,000 operations, including routine works, maintenance and trouble-shooting, and are promoting safety measures for high risk operations.
In addition to risk assessment of new facilities, we also continue to hold practical trainings for risk assessment to enhance risk assessment of existing facilities and ensure risk assessment of chemical substances. - Compliance with safety rules with health and
safety patrols
In addition to monthly health and safety patrols conducted at each office and group company, executive in charge of health and safety and the chairperson of the labor union tour all production bases in Japan for health and safety patrol to ensure the compliance of safety rules in time for the National Safety Week every July. We set October 7 as “Bando Safe Day,” and on that day every year, the President sends a message about safety to all employees, and all directors, including the President, conduct a health and safety patrol to check routine health and safety activities. - Promotion of safety measures for
facilities
We are implementing measures to prevent accidents related to manual interventions that frequently occur in non-routine works and also to make necessary changes to facilities to ensure the safety of workers even in non-routine works. We compiled examples of safety measures and use them to check safety and make improvement of facilities. - Safety sensitivity improvement training using
disaster simulation equipment
We provide a training on safety sensitivity to enhance employees’ sensitivity to risks inherent to their works through a simulation of potential accidents, such as being caught or stuck in machines, that are likely to occur at the Group’s production facilities. We expanded the scope of this training to the entire Group since fiscal 2014 and installed disaster simulation equipment in all of domestic plants and affiliates as well as in 10 major overseas production bases to promote similar training.
As a result, Nankai Plant achieved a record of 8,400,000 hours of accident-free operation in November 2020 and received the "Minister of Health, Labour and Welfare's Special Award for Outstanding Foremen in Occupational Safety" in December 2020. Overseas, we received the National Occupational Safety and Health Award from the Ministry of Labour of Thailand in October 2020.
Bando Safe Day
Press vulcanization equipment with a safety fence
Safety sensitivity improvement training